Zeolite World
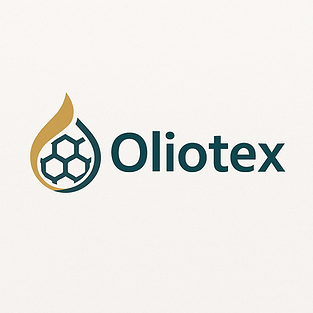
Oliotex Data Sheet (English)
Industrial Oils: Broader Applications
Industrial processes frequently use thermal oils, hydraulic fluids, and lubricants at high temperatures — all of which degrade over time due to oxidation, contamination, or thermal breakdown. These include:
-
Heat transfer fluids in solar power, plastics, and textile manufacturing
-
Hydraulic oils in machinery, presses, and elevators
-
Lubricants in high-speed mechanical systems
Contaminants such as oxidized compounds, metal particles, water vapor, and acids accumulate, degrading performance, corroding equipment, and requiring premature oil replacement.
How Oliotex Adapts
The core technology in Oliotex— nano-refined, surface-activated natural zeolite — can be:
-
Modified by pore size and surface polarity to target specific contaminants
-
Thermally stabilized for higher temperature resistance
-
Packaged in custom modules (e.g., cartridge filters, bed reactors) for inline industrial systems
This allows the same adsorption mechanism that works in cooking oil to be engineered for oils operating at 150–400°C or higher, selectively trapping unwanted compounds while leaving the oil's core functionality intact.
Benefits in Industry
By integrating Oliotex into industrial oil loops, users could see:
-
Extended oil service life (cutting costs on replacement fluids)
-
Improved equipment protection (less wear from micro-contaminants)
-
Increased process stability (especially in precision applications)
-
Reduced environmental impact (lower oil waste volume)
A Platform for Custom Engineering
Oliotex isn’t just a product — it’s a platform material. With targeted R&D, versions of Oliotex could be custom-designed for sectors like:
-
Automotive & aerospace (synthetic lubricant purification)
-
Petrochemicals & refineries (residual oil purification)
-
Renewable energy (solar thermal systems, ORC fluids)